Ultrasonic cavitation
Ultrasonic cavitation is the phenomenon whereby the principle of ultrasonic cleaning can be understood. In a liquid medium the ultrasonic waves, generated by an apposite electronic ultrasounds generator and a special transducer suitably mounted under the bottom of a stainless steel tank, produce compression and vacuum waves at a very high speed, the speed depending on the working frequency of the ultrasounds generator. They normally work at a frequency between 28 and 50 kHz. The pressure and vacuum waves in the liquid cause the phenomenon known as "ultrasonic cavitation".
Surface tension, viscosity and vapour pressure
In order to gain a better understanding of the phenomenon, we have to refer to some basic concepts such as "surface tension", "viscosity" and "vapour pressure or tension". Liquids are in fact characterised by the fact that the particles have much greater potential for movement than in solids, albeit subject to much higher forces of attraction than those in gases. More particularly water is a molecular liquid, evaporates at all temperatures but boils at a well-defined one, i.e. at the "boiling point" which for distilled water is 100 degrees centigrade, at which the vapour pressure reaches the value of 1 atmosphere.
The formation of cavities and the implosion phenomenon
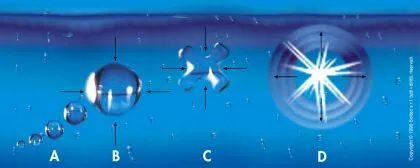
What happens when we subject a certain quantity of water at room temperature to an intense ultrasonic field? During the vacuum phase (see Fig. 1 phase A) numerous bubbles of gas are formed in the liquid and which enlarge for the duration of the acoustic vacuum phase (negative pressure). This formation of microscopic bubbles of gas is the start of cavitation (i.e. the formation of gaseous cavities in the liquid). During the second phase of ultrasonic compression (see Fig. 1 phase B), the enormous pressure exerted on the newly expanded bubble compresses the same, hugely increasing the temperature of the gas contained in it (see Fig. 1 phase C) until the bubble collapses on itself, imploding with a consequent vast release of impact energy (see Fig. 1 phase D). The impact energy caused by implosion of the gas bubble hits the surface of the object to be cleaned, interacting both physically and chemically. In physical terms a "micro brushing" effect is achieved at very high frequency (around 50,000 times per second for a machine operating at 50 kHz) with, in chemical terms, the cleansing effect of the chemical substance present in the detergent of the ultrasonic bath.
Choosing the type of detergent and the working temperature
As we will see, consideration also of the chemical and physical aspect of the type of detergent used in an ultrasonic cleaner is of fundamental importance, and account has to be taken of many parameters when choosing an ultrasonic cleaner and detergent. The first is the type of substance to be removed from the soiled object and consequently the choice of the type of chemical substance which can attack the contaminant. Clearly the chemical substance (detergent), used in order to cavitate efficiently, must be an aqueous solution, possibly with high vapour pressure and low surface tension, and must be used at a working temperature of around 50-60°C. The temperature of the aqueous solution in an ultrasonic cleaning bath is very important, as the cavitation intensity varies as the temperature varies. It also increases as the temperature increases up to around 70°C and then decreases and stops completely at the temperature of boiling of the liquid. Another important parameter to be considered is the vapour pressure of the detergent solution used. Vapour tension or pressure refers to the following concept: if we consider a liquid in a closed and temperature-controlled recipient, the surface molecules which have sufficient energy change to the vapour state and occupy the available space above the liquid. Occasionally some vapour molecules return to the liquid state until, when the state of equilibrium of the system is reached, at a constant temperature, the speed of evaporation equals that of condensation. The pressure exerted by the vapour molecules, in these conditions, is defined as vapour tension. Its value does not depend on the quantity of liquid present but only on the temperature. Therefore, if a liquid is heated, the vapour tension increases with the temperature and when the vapour tension equals the external pressure the phenomenon of boiling takes place. Each liquid therefore has its own vapour pressure and a different boiling point. Ethyl alcohol for example will have a much higher vapour pressure than that of water at the same temperature: it boils at 78°C and at the boiling point will have a vapour pressure of 1 atm, while water boils at 100°C with a vapour pressure of 1 atm. Normal boiling point defines the temperature at which the vapour tension of the liquid equals the pressure of 1 atm. A proper understanding of the concept of vapour pressure is important in that it plays a major role in the cavitation process. The energy required for forming a cavitation bubble is proportional both to the vapour pressure of the liquid and the surface tension value. Cavitation is difficult when the vapour pressure of the liquid is low (cold water). Contrarily the cavitation bubbles implode with greater energy, although the power applied has to be increased considerably in order to reach the minimum cavitation threshold. Therefore the result is generally a smaller formation of bubbles and a smaller number of implosions. For example an increase in the temperature of the liquid raises the vapour pressure of the same, making vapour cavitation easier. Therefore a high vapour pressure lowers the minimum cavitation threshold, creating many more bubbles which collapse, imploding with a lower energy in that the difference between internal and external pressure is smaller. The viscosity of the liquid should also be taken into consideration. High viscosity values prevent cavitation, while low viscosity values allow diffusion of the ultrasonic waves and therefore the formation of cavitation bubbles. Similarly liquids with high and low surface tension values behave in the same way as those with high or low viscosity value as described above.
Sweep system: technology and benefits
Other important parameters for achieving good levels of cavitation in a liquid are the frequency of the ultrasounds generator, the power, the use of the SWEEP SYSTEM generator and finally the type of transducer used. The frequency of the ultrasounds generator is important in that it determines the size of the gas bubble in the liquid subjected to ultrasonification. The higher the frequency of the generator, the smaller the size of the cavitation bubble generated; contrarily the lower the frequency, the greater the size of the bubble. Clearly a larger bubble will require greater energy to implode and consequently will also have greater impact energy, while a smaller bubble will need less energy to implode and consequently has lower impact energy. What is then the benefit of using ultrasonic cleaning systems with high frequencies? High frequencies allow many more bubbles to be generated in the unit of time, enabling better cavitation distribution per surface unit. For example, in a 40 kHz system, the distance between the nodes and antinodes (or loops) of the acoustic wave is practically double that generated by 20 kHz systems. Therefore 40 kHz systems generate in the unit of time many more bubbles, above all smaller in size, allowing even very small points to be reached per surface unit. To give a practical example, we can compare fine cavitation at high frequency to very fine-grained sandpaper, while low frequency cavitation can be compared to very coarse-grained sandpaper. The purpose of the sandpaper is that of abrading, however very different results can be obtained according to whether a fine-grained or coarse-grained type is used. The type of generator used can be piezoelectric or magnetostrictive. Piezoelectric transducers are normally used in that they can be designed with much higher frequencies compared to the magnetostrictive type. High-power magnetostrictive transducers do not exceed 22 kHz. Finally the use of a SWEEP SYSTEM generator allows a further improvement in distribution of ultrasonic cavitation. The frequency of the generator is modulated around a central frequency with 1 kHz increases or decreases. For example a transducer piloted at 40 kHz will oscillate at a frequency between 39 and 41 kHz. This frequency variation prevents formation in the liquid of the so-called "stationary waves" which can generate acoustic interference when two (or more) wave trains intersect in a given region of the space. The SWEEP SYSTEM therefore reduces cleaning times, prevents damage to delicate parts, considerably increases the distribution of ultrasonic cavitation and facilitates its process in liquids which cavitate with difficulty. The SWEEP SYSTEM is normally used in industrial and highly professional cleaning systems, however nowadays some producers are starting to supply it on small ultrasonic cleaning units too.